The Brevik CCS-project is on track!
As we recently entered a new year, I would like to give some insights after one year with Brevik CCS says Tor Gautestad, Project Manager of Brevik CCS.
-Firstly, I would like to mention that the progress is good and according to schedule on all critical activities. An important notation for us is that we still maintain the zero’s on all the key parametric on health and safety:
Zero serious injuries, zero activities that leads to loss of working time (LTI’s), zero activities that needs medical treatment (MTI’s), zero activities leading to considerable emissions to environment, zero activities with considerable damage to assets, and we haven’t had any reported sick leaves related to the project.
We are of course proud of these positive results, but with the focus and efforts we put into health and safety we expect nothing less also for the remaining of the project.
Demanding work
However, it must be stated that the project work is indeed demanding. The first few months of construction work were vastly influenced by the fact that we are working on a „brownfield“-area. (Editor’s note: Brownfield is a term used to describe an area that is being developed on a place previously used is some other setting.)
The challenge for us here has been that the area we’re working in, has been industrialized since the early 1920’s where Norcem already had a large footprint in the area, and since then the factory has been rebuilt several times. This leads to frequent finding of old pipes, cables, foundations and poles. On the positive side, we can now see the light in the tunnel and I believe we’ve been through the toughest parts related to the “brown field” issues.
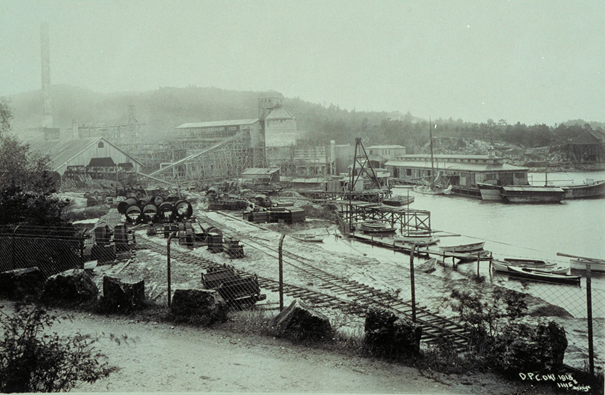
And adding the continuous challenges from the pandemic on top of this, I think it is quite an achievement that we have managed to still be on schedule..
As most of you have probably read in the news, we’ve had some serious challenges related to costs. The magnitude of the mentioned challenges have been bigger than we forecasted, and we have had several unforeseen and costly tasks added into the project. On top of this the pandemic has created some additional challenges, since the unit prices of several important input factors has risen sharply. We obviously would have preferred avoidance of this overrun but given the circumstances we cannot see how the additional costs could have been mitigated.
Valuable key learnings
One important “lessons learned” has been that we were too optimistic in the cost/risk-analysis conducted under the FEED-study, which led to too low reserves in the budget. Throughout the past 12 months of the project we’ve also gained important insights into how to construct a new factory into an old existing plant, and the learning's here can be helpful for other plants, both within our industry, and others in the future. I’m sure that many other factories and plants will have the same challenges, as they seek transformation to a more sustainable cement production.
It has also been very demanding to run a large partially state-subsidized project. There are a lot stakeholders in this project, and the project carries a lot of attention, both locally, nationally and globally.
The key insights we’ve met here will be very valuable for future projects, and I’m therefore optimistic about the new budget proposal now being discussed, and I strongly believe that this will carry us through the project.
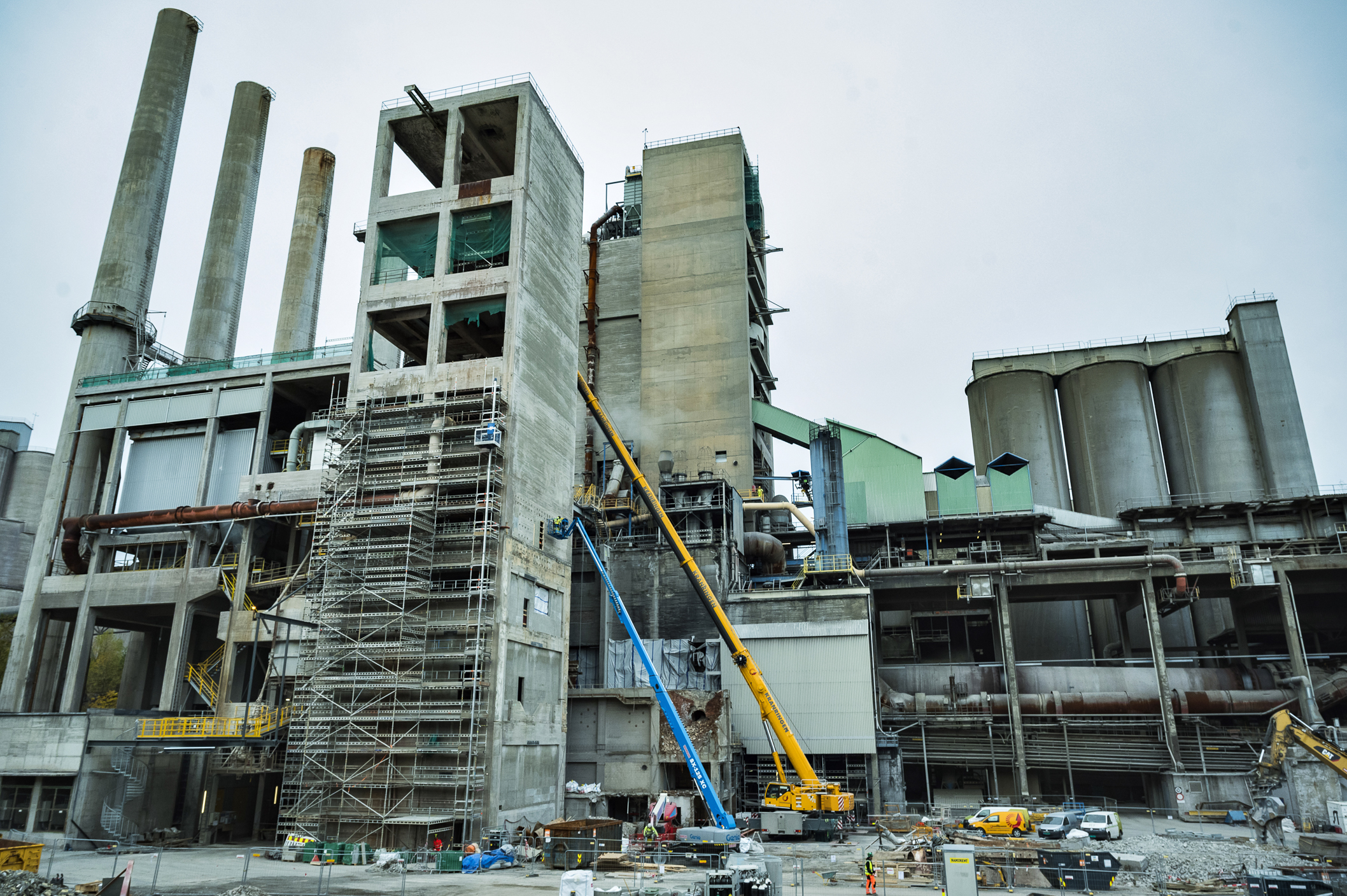
Dag Jenssen /norcem
Some specifics
Throughout the last period we’ve also decided to move the future shipping dock where we will transport the fluid CO2, from “Grenland Havn”, to our own harbour called „Sekkekaia “. This change has been important both for Norcem Brevik, and for Brevik CCS, and we will soon be closing all remaining clarifications raised by Northern Lights. The change will include a full upgrade of the „Sekkekaia“, and will be conducted in 2022, nearly 100 years after it was built.
Whilst I’m writing this, we are also about to remove the last traces of cement kiln No 4 in Brevik. The kiln was originally started in 1956, and permanently stopped in 1982. The manufacturer of the kiln was Polysius, and it had a capacity of 500 tons clinker per day. The demolition of this has had some extra-ordinary challenges, since the process equipment was not emptied, and in addition it was found asbestos in some parts of the construction. The result was that the demolition became far more comprehensive and costly that estimated.
Contracts
We’ve recently contracted three new civil work packages. The so-called C1c-contract has been contracted with Helge Klyve, where they will build the foundations for the large heat exchangers and the the electrostatic precipitator No 3, in addition to the transformer building Infront of the tower of oven 5. Helge Klyve also had the contract for the preparational work (contract C0) which is now practically completed. It must be stated that it is a vote of confidence that we’ve given them a new contract.
Secondly has Tor Entreprenør been awarded a contract for the establishment of foundation to the new maintenance center. This is being executed at this early stage to save time towards the end of the project when the actual building is being raised. The building contract is as many know, postponed until after the process plant is closed in early 2024.
The third contract that was been agreed upon, is the C2-contract signed with NRC for establishing the new „Cementine“-jetty. The old jetty has already been demolished, and we need to establish a new one that can carry the weight of the heaviest components to the new process plant, to be brought to the jetty by barge. Ongoing works includes stone filling and soon piling. Thereafter we will start the casting process.
Busy time ahead
We are also moving towards the main revision for 2022, which will undoubtably become a challenging period for us, since we’re replacing the electrostatic precipitator No 3 and the ID fan No 2 in the area we call „Wall Street“.
There are a lot of cables that needs to be rerouted in this area, which made it necessary to extend the revision by one week.
I hope that this post have given you some more knowledge and insight into the Brevik CCS-project.
If you have any questions, please be in contact.